|
High Speed Rail IDEA Project 32 [Completed (IDEA)]
High-Strength, Lightweight Car Bodies for High-Speed Rail Vehicles
Project Data |
Funds: |
$96,703 |
Staff Responsibility: |
Chuck Taylor |
Completion Date: |
1/1/2004 |
Fiscal Year: |
2001 |
|
This project examined a novel approach for building safer high-performance, high-speed passenger car shells. The objective was to evaluate the potential of using scandium-containing aluminum alloys in combination with advanced joining and fabrication approaches to increase performance, reduce operating costs, and improve the safety of high-speed passenger rail vehicles. The approach combined three key elements 1) light-weight, high-strength, weldable aluminum scandium alloys; 2) advanced joining techniques (friction stir welding); and 3) advanced processing to fabricate net-shaped panels. A major task was to select the optimal scandium-containing aluminum alloy composition for high-speed passenger rail applications. At present, aluminum scandium alloys are seeing widespread use in “high tech” sporting good products such as ball bats, bicycles, golf clubs, and lacrosse poles. Although this family of alloys is now available commercially, it has not been optimized or qualified for use in rail passenger vehicles.
Scandium provides the highest increment of strengthening per atomic percent of any alloying element when added to aluminum. Small amounts of scandium are very effective at improving mechanical properties and refining the microstructure of wrought aluminum alloys. In addition, scandium additions have been shown to improve weldability of aluminum alloys by reducing hot cracking in the weld region. In the current study,researchers performed a trade-off study to determine if scandium additions would improve the performance of conventional Al-Mg 5XXX and Al-Mg-Si 6XXX alloys and if a scandium containing Al-Zn-Mg-Cu 7XXX series alloy could be used to fabricate car body shells.
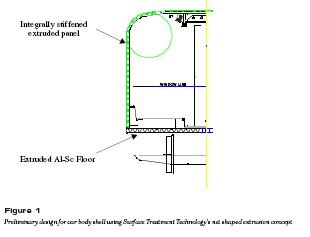
The final report for this IDEA project can be found at:
|
|