This contract investigated the application of a magnetorheological (MR) damper in place of a conventional hydraulic shock retarder in spring rail frog switches. The spring rail frog switch is used in mainline track where the preponderance of traffic is through trains with only occasional diverging route usage for passing sidings or infrequently used industry tracks (see Figure 1). The spring rail frog switch is useful for this service because no power machinery is required and manual throwing of the switch machine is required only for train entry. The spring rail frog switch closes against the frog after the trailing axle of each car truck using the force of the springs in the system (see Figure 1). However, the cycling action of the spring rail frog switch contributes to rapid wear and loosening of the entire system. Currently, hydraulic retarders are used to minimize cycling of the spring rail frog switch against the point-of-frog as trains exit spring switches. These hydraulic retarders (shock absorbers) are used to keep the spring rail away from the frog for extended periods to allow multiple car trucks to pass. Railroads report that the current retarder system does not have a reliable or long life due primarily to high internal forces in the retarder during train passage.
An MR damper resembles an ordinary hydraulic shock absorber. However, it uses a special MR fluid and has one or more electromagnetic coils wrapped around the piston head. The MR fluid contains small magnetically polarizable particles. As a result, when current is supplied to the coils, the MR fluid becomes semi-solid. Damping is proportional to the amount of current applied. If sufficient current is supplied, the MR damper could “clamp” open the spring rail until most or all cars in a train have passed, substantially reducing wear on all components. The MR system includes a control algorithm designed to prevent or minimize cycling of the spring rail until the train has passed through. An accelerometer attached to the piston rod detects the acceleration and velocity of the rod when activated by a passing train. The sensor signal is used by the algorithm to activate the MR damper and determine the amount of damping required. A battery kept charged by solar cells provides power to the system.
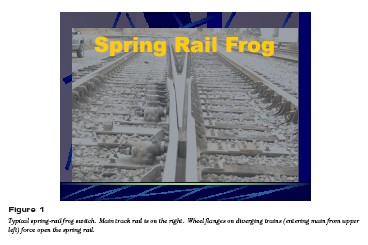