This project is investigating the use of electroslag welding (ESW) techniques as an alternative to thermite or flashbutt welding for field welding of rails. Heat is generated by resistance as the welding current passes through a molten flux pool that floats on top of the liquid metal. Containment components, e.g., cooling shoes on the sides of the rails, are used to contain the welds, and a consumable electrode directs weld wire to the weld.
Electroslag welding has the potential to produce a stronger, better quality weld than the current thermite field welding process.
The investigative approach included developing an efficient electroslag welding process. Elements of that process include consumable electrode configuration, starting sump design, weld chemistry, welding parameters (volts, amps, travel speed, wire feed, etc.), flux, and cooling requirements. Alternative weld wires, fluxes, and cooling shoe materials will be selected, as well as various configurations of consumable guide tubes, cooling shoes, and fixturing. The most promising was then used to weld test rail segments, and these welds evaluated using ultrasonic inspection and destructive testing based on American Railway Engineering and Maintenance of Way Association specifications. Metallographic specimens of the weld were prepared to examine weld and heat-affected zone dimensions and microstructures, and weld specimens were tested for hardness.
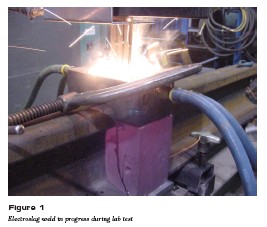
The final report for this IDEA project can be found at: