This project developed and tested prototype devices and methods to clean electrified third rail insulators for rail rapid transit systems. Dirt and grime can short circuit the insulator and cause arcing, burning, and smoke, which can cause the rail system to be shut down. The insulators are extremely difficult to clean because the third rail carries very high voltage, and the third rail cover and tunnel walls limit access to the insulators. Figures 1 and 2 show examples of these problems on different transit systems. This project included development, proof of concept, and prototype testing of the cleaning devices to address the problems.
The prototype device was developed and attached to a service vehicle and tested on the Washington Metropolitan Area Transit Authority (WMATA) Metrorail system and the Maryland Transit Administration (MTA), Baltimore rail rapid transit facilities. The following transit agencies participated in this project by providing staff review and guidance: the San Francisco Bay Area Rapid Transit District (BART), Chicago Transit Authority (CTA), New York City Transit (NYCT), Metropolitan Atlanta Rapid Transit Authority (MARTA), Southeastern Pennsylvania Transportation Authority (SEPTA), and the Massachusetts Bay Transportation Authority (MBTA). These agencies have also indicated a need for a third rail insulator cleaning.
Dirty insulators are among the most frequent causes of downtime in many rail rapid transit systems around the country. Aging infrastructure and insulators of different sizes, shapes, and materials pose challenges. The insulator cleaning devices have the potential to improve the safety and security of rail transit systems and enhance public perception and confidence in the security of these transit systems.
Rail rapid transit systems routinely replace thousands of burnt out insulators every year at considerable cost. Cleaning insulators is especially difficult and costly inside tunnels where there is no rain to wash away dust and nowhere for combustible debris and smoke to go. In one agency, about 4000 insulators failed per year inside tunnels and about 100 outside tunnels. Tunnels often have water drips creating lime deposits and higher humidity. This condition speeds up rusting and corrosion of metal bases, caps, and retaining rings on insulators and accelerates failure. Rail rapid transit systems use power supplied by a third rail that sits on insulators, which are typically spaced about 10 feet apart. Most rail rapid transit systems have an overrunning electrical collector shoe above the third rail. Carbon dust from carbon brushes on the traction motor, rust particles, dirt, and grime can short circuit the insulator, cause smoke, and set wood ties on fire, which can shut down train operation. If the insulator is made of fiberglass, it can burn. Porcelain insulators can become red hot and melt. When a porcelain insulator flashes over, it can explode and the resulting plasma ball can have a temperature of up to 5000 °F and can vaporize a concrete tie and rebar. Because of environmental considerations, chemical cleaning agents are generally not allowed. Stray currents, caused by partially shorted insulators, can corrode gas and water mains in the tunnels.
Rail rapid transit systems routinely replace thousands of burnt-out insulators every year at considerable cost. Cleaning insulators is especially difficult and costly inside tunnels where there is no rain to wash away dust and nowhere for combustible debris and smoke to go. In one agency, about 4,000 insulators failed per year inside tunnels and about 100 insulators failed in outside tunnels. Tunnels often have water drips creating lime deposits and higher humidity. This condition speeds up rusting and corrosion of metal bases, caps, and retaining rings on insulators and accelerates failure. NTIS #PB2005-107675.
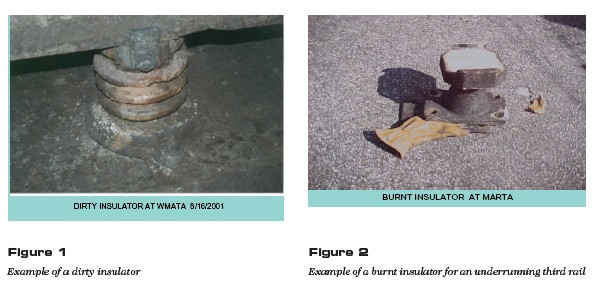
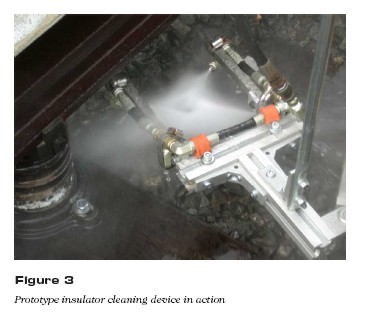
Project Results
This Transit IDEA project has developed and successfully demonstrated a prototype cleaning device. Bench tests were conducted to evaluate the potential performance of several insulator surface cleaning technologies: (1) pneumatic polishing with rice husks with high silica content, (2) mechanical cleaning with powered rotating brushes, and (3) pressure washing with high temperature tap and deionized water. Pressure washing with hot tap water was the most appropriate cleaning tool.
A U-shaped cleaning station with four spray nozzles was attached via primary and secondary arms to a service vehicle. Electric power must be shut off before this device can be used.
The cleaning system was developed into a prototype that was mounted on a service vehicle driven on the tracks, and tested and evaluated at MTA in Baltimore and WMATA in Washington, D.C., rail rapid transit facilities. BART, CTA, NYCT, MARTA, SEPTA, and MBTA participated in this project and provided guidance to the principal investigator. The final report included information so that other rail rapid transit agencies can consider using this device for cleaning their third rail insulators.
Project Payoff Potential
The cleaning device could offer rail rapid transit agencies an effective method to efficiently and cost-effectively clean dirty insulators in place, improving the safety and reliability of those transit systems.
Product Transfer
The prototype insulator cleaning device was tested on the WMATA Metrorail and the MTA, Baltimore rail rapid transit systems. The results were included in a final report for this project and will be disseminated by the principal investigator via papers presented at symposia, professional meetings, and TRB and APTA conferences. The results of this project were presented at the APTA Rail Conference in June 2006. The participation of the eight transit agencies identified above will make the results useful to transit systems with different kinds of third rail insulators.
Building on this project, a follow-on Phase 2 project, to develop a higher-speed operational cleaning device, was conducted. That Phase 2 project is Transit IDEA Project 47. The principal investigator plans to show the insulator cleaning devices to transit agencies and equipment manufacturers for potential commercialization.
The final report for this IDEA project can be found at:
https://onlinepubs.trb.org/onlinepubs/archive/studies/idea/finalreports/transit/Transit36_Final_Report.pdf.